Real-World Insights Into the Implementation of Quality Management Systems (Qms)
In today's fast-paced and competitive business environment, maintaining quality standards is crucial for organizations to thrive. However, implementing a Quality Management System (QMS) is not always a straightforward process. It requires careful planning, execution, and constant monitoring to ensure its effectiveness. In this discussion, we will explore real-world insights into the implementation of QMS, uncover the key components of a successful implementation, and discover best practices for overcoming challenges. Additionally, we will delve into real-world examples of organizations that have successfully implemented QMS and explore how they measure and improve its performance. Join us as we unravel the complexities of quality in action and uncover the secrets to achieving excellence in QMS implementation.
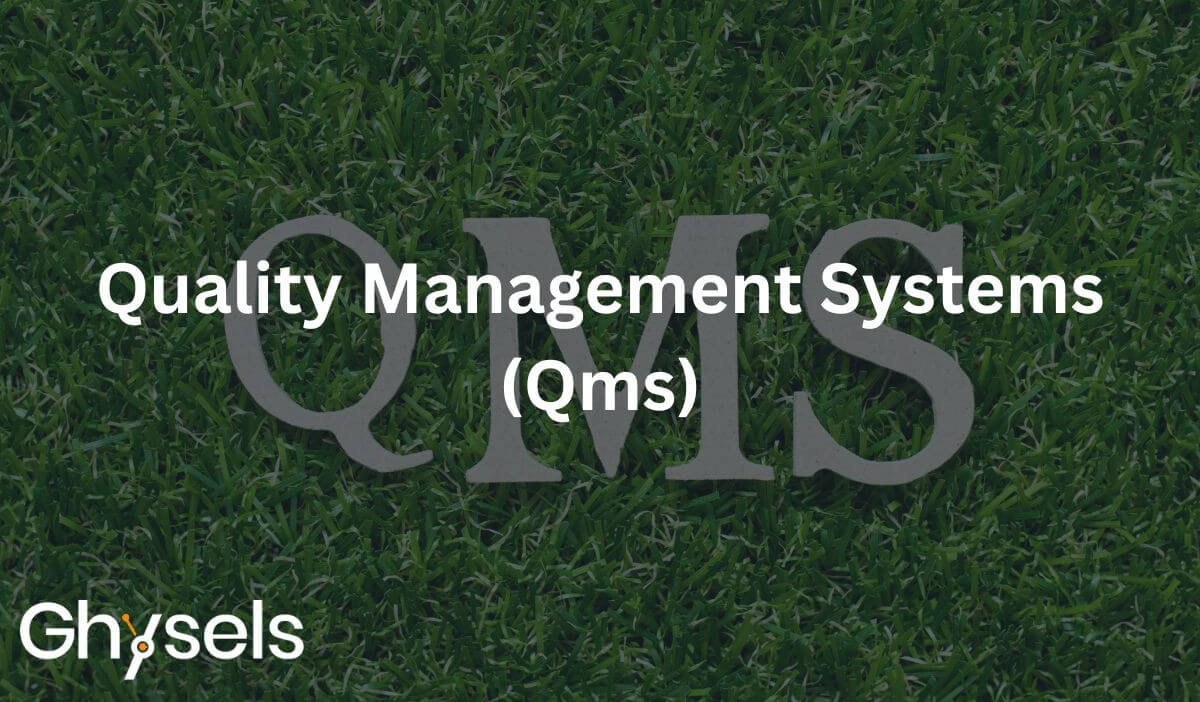
Key Takeaways
- QMS plays a crucial role in enhancing customer satisfaction, improving operational efficiency, managing risks, and ensuring well-defined processes.
- Leadership is vital in the successful implementation of QMS, including setting a clear vision, establishing a culture of quality, actively participating in development, providing guidance and resources, and inspiring employees to embrace QMS and drive continuous improvement.
- Continuous improvement is essential in QMS, involving regular evaluation of processes, identifying areas for improvement, adapting to changing business environments, staying competitive, and meeting customer expectations.
- Training and education are crucial for the successful implementation of QMS, ensuring employees understand principles and processes, acquiring necessary knowledge and skills, creating a culture of quality, and contributing to the success of QMS.
- Auditing and compliance are integral parts of QMS, conducting regular internal audits to identify deviations, ensure compliance with quality standards, identify areas for improvement, maintain integrity, and enable corrective actions.
Understanding the Importance of QMS
Understanding the Importance of QMS is crucial for organizations seeking to improve their overall quality and effectiveness. Implementing a Quality Management System (QMS) provides numerous benefits for businesses, including enhanced customer satisfaction, increased operational efficiency, and improved risk management. QMS ensures that processes are well-defined and consistently followed, leading to better product or service quality.
The role of leadership in QMS is integral. Leaders must set a clear vision and establish a culture of quality within the organization. They should actively participate in the development and implementation of QMS, providing guidance and resources to ensure its success. By demonstrating their commitment to quality, leaders inspire employees to embrace the QMS and drive continuous improvement.
Continuous improvement is a fundamental aspect of QMS. It involves regularly evaluating processes, identifying areas for improvement, and implementing corrective actions. This iterative approach helps organizations adapt to changing business environments, stay competitive, and meet customer expectations.
Training and education play a vital role in QMS implementation. Employees need to understand the principles and processes of QMS to effectively contribute to its success. By providing comprehensive training programs, organizations ensure that employees have the necessary knowledge and skills to perform their roles within the QMS framework.
Auditing and compliance are key components of QMS. Regular internal audits help identify deviations from established processes and ensure compliance with quality standards. By conducting audits, organizations can identify areas for improvement and take corrective actions to maintain the integrity of the QMS.
Key Components of a Successful QMS Implementation
To successfully implement a Quality Management System (QMS), organizations must carefully consider the key components that contribute to its effectiveness and overall success. These components include implementation strategies, system integration, training requirements, documentation management, and continuous improvement.
Firstly, organizations need to develop effective implementation strategies to ensure a smooth transition to the QMS. This involves creating a detailed plan that outlines the steps, timelines, and responsibilities for each phase of the implementation process.
Secondly, system integration is crucial for a successful QMS implementation. This involves integrating the QMS into existing business processes, systems, and technologies. By aligning the QMS with the organization's operations, it becomes easier to monitor and control quality throughout the entire value chain.
Thirdly, organizations must invest in training programs to ensure that employees understand and adhere to the QMS requirements. This includes providing comprehensive training on quality principles, processes, and tools. By educating employees, organizations can create a culture of quality and empower individuals to actively contribute to the success of the QMS.
Furthermore, effective documentation management is essential for a successful QMS implementation. This involves establishing processes for document control, version control, and record keeping. By maintaining accurate and up-to-date documentation, organizations can ensure compliance with regulatory requirements and enable effective decision-making.
Lastly, continuous improvement is a key component of a successful QMS implementation. Organizations should establish mechanisms for monitoring, measuring, and analyzing quality performance. By identifying areas for improvement and implementing corrective actions, organizations can continuously enhance their QMS and achieve higher levels of quality.
Overcoming Challenges in Implementing a QMS
Implementing a Quality Management System (QMS) can present various challenges that organizations must overcome to ensure its successful implementation. These challenges require careful planning and execution to ensure that the QMS is effectively integrated into the organization's processes and culture. Here are four key challenges that organizations may face when implementing a QMS:
- Change management: Implementing a QMS involves significant changes to existing processes and workflows. Resistance to change is natural, and organizations must proactively manage this resistance by clearly communicating the benefits of the QMS and involving employees in the implementation process.
- Stakeholder engagement: Engaging stakeholders, including employees, customers, and suppliers, is crucial for the success of a QMS implementation. Organizations should actively involve stakeholders in the decision-making process, seek their feedback, and address their concerns to foster a sense of belonging and ownership.
- Employee training: To ensure the effective implementation of a QMS, employees need to be trained on the new processes, procedures, and tools. Training programs should be comprehensive, tailored to the specific needs of different job roles, and ongoing to support continuous improvement.
- Documentation control: Maintaining accurate and up-to-date documentation is essential for a QMS. Organizations must establish robust document control processes to ensure that the right documents are available to the right people at the right time, facilitating compliance and continuous improvement.
Best Practices for Ensuring QMS Effectiveness
One crucial aspect of ensuring the effectiveness of a Quality Management System (QMS) is to establish clear objectives and performance indicators. These serve as a roadmap for the organization to continuously improve its processes and outcomes. Another important practice is stakeholder engagement, which involves actively involving all relevant parties in the design, implementation, and evaluation of the QMS. This ensures that the system meets the needs and expectations of all stakeholders, fostering a sense of belonging and ownership.
Training and education are also key factors in QMS effectiveness. By providing employees with the necessary knowledge and skills, they can effectively contribute to the implementation and maintenance of the QMS. This can be achieved through various training programs, workshops, and certifications.
Documentation management is another best practice that ensures QMS effectiveness. It involves establishing a systematic approach to create, manage, and control all documentation related to the QMS. This includes policies, procedures, work instructions, and records. Proper documentation management facilitates compliance with regulatory requirements and enables efficient communication and decision-making.
Lastly, conducting regular risk assessments is essential for maintaining QMS effectiveness. This involves identifying potential risks and taking proactive measures to prevent or mitigate them. By addressing risks promptly, the organization can avoid disruptions, enhance process efficiency, and ensure the delivery of high-quality products and services.
Real-World Examples of Successful QMS Implementations
Building upon the best practices for ensuring QMS effectiveness, real-world examples demonstrate the successful implementation of Quality Management Systems (QMS) in various industries and organizations. These case studies serve as industry benchmarks, showcasing how organizations have achieved customer satisfaction, continuous improvement, and regulatory compliance through the implementation of a robust QMS. Here are four examples that highlight the successful outcomes of QMS implementations:
- XYZ Corporation: By implementing a QMS, XYZ Corporation achieved significant improvements in customer satisfaction. Through enhanced processes and a focus on meeting customer needs, the company saw a 20% increase in customer satisfaction ratings within six months.
- ABC Manufacturing: ABC Manufacturing implemented a QMS to ensure regulatory compliance and improve product quality. As a result, they experienced a 30% reduction in product defects and a 15% increase in customer retention rates.
- PQR Healthcare: With the implementation of a QMS, PQR Healthcare achieved continuous improvement in patient care. By analyzing data and implementing corrective actions, they reduced medication errors by 40% and improved patient outcomes.
- LMN Financial Services: LMN Financial Services implemented a QMS to streamline processes and improve efficiency. This resulted in a 25% reduction in processing time, allowing the company to handle a higher volume of transactions and improve customer satisfaction.
These real-world examples demonstrate the tangible benefits and positive impact of implementing a QMS, emphasizing the importance of quality management in achieving organizational success.
Measuring and Improving QMS Performance
To ensure the effectiveness and success of a Quality Management System (QMS), it is essential to establish a comprehensive framework for measuring and improving its performance. This involves the use of performance metrics, continuous improvement, data analysis, process optimization, and employee engagement.
Performance metrics play a crucial role in measuring the performance of a QMS. These metrics can include customer satisfaction scores, defect rates, on-time delivery, and adherence to quality standards. By regularly monitoring these metrics, organizations can identify areas for improvement and track progress over time.
Continuous improvement is a fundamental principle of a QMS. It involves regularly reviewing processes, identifying areas for improvement, and implementing changes to enhance efficiency and effectiveness. This can be achieved through techniques such as root cause analysis, corrective and preventive actions, and regular audits.
Data analysis is another important aspect of measuring and improving QMS performance. By analyzing data collected from various sources, organizations can identify trends, patterns, and areas of concern. This helps in making data-driven decisions and implementing targeted improvement initiatives.
Process optimization involves streamlining and improving processes to eliminate waste, reduce errors, and enhance overall performance. This can be achieved through techniques such as lean manufacturing, Six Sigma, and value stream mapping.
Employee engagement is crucial for the success of a QMS. Engaged employees are more likely to be committed to quality, actively participate in improvement efforts, and contribute innovative ideas. Organizations should foster a culture of continuous improvement and provide training and development opportunities to enhance employee skills and knowledge.
Frequently Asked Questions
What Are the Potential Consequences of Not Implementing a Qms?
The potential consequences of not implementing a QMS include cost implications, legal and regulatory non-compliance, increased customer complaints, inefficient processes, and decreased customer satisfaction. These outcomes can negatively impact an organization's performance and reputation.
How Can a Company Ensure Employee Engagement and Buy-In During the QMS Implementation Process?
To ensure employee engagement and buy-in during the QMS implementation process, companies should focus on employee motivation, effective change management, communication strategies, well-designed training programs, and strong leadership involvement. These factors contribute to a sense of belonging and commitment to the implementation process.
Are There Any Industry-Specific Challenges or Considerations That Should Be Taken Into Account When Implementing a Qms?
Industry-specific challenges and considerations must be taken into account when implementing a QMS. These may include regulatory compliance, process integration, and stakeholder involvement. It is crucial to address these factors to ensure successful implementation and quality outcomes.
What Are Some Common Pitfalls or Mistakes That Companies Make During the QMS Implementation Process?
During the QMS implementation process, companies commonly make mistakes such as lack of employee engagement, failure to consider industry-specific challenges, and inadequate continuous monitoring and evaluation. These pitfalls can have consequences on the effectiveness of the system and ongoing improvement efforts.
How Can a Company Continuously Monitor and Evaluate the Effectiveness of Their QMS to Ensure Ongoing Improvement?
Continuous improvement of a Quality Management System (QMS) requires monitoring and evaluating its effectiveness. This can be achieved through performance metrics, customer satisfaction surveys, process analysis, and technology integration to identify areas for ongoing improvement.
Conclusion
In conclusion, implementing a Quality Management System (QMS) is crucial for organizations to ensure quality in their operations. This article has provided insights into the importance of QMS, key components for successful implementation, challenges faced, best practices for effectiveness, and real-world examples of successful implementations. By measuring and improving QMS performance, organizations can continuously enhance their quality standards and meet customer expectations.